This project was started in my senior year of high school. From a young age I had always been inspired by innovators from the early 20th century such as Henry Ford and William Harley. In particular I have always been fascinated by their abilities to take what they had and use their imaginations to create something spectacular. The fact that they were able to create motorcycles and cars with tools and machinery more than 100 years ago always made me think “why can’t I do the same.” So being in highschool and wanting a mode of transportation faster than my bicycle and not being able to afford a car created the perfect atmosphere for me to create the motorized bike.
I started off with a used 1970s Schwinn cruiser bicycle and a 5hp Sears tiller with a briggs and stratton gasoline engine. With a tight budget that was all I was able to afford. Luckily I had the privilege to work in my friends garage and use his tools. I had access to basic hand tools, a drill press, a band saw, angle grinder, and a mig welder. That, a whole lot of trial and error, and a never ending drive helped me create a running motor bike. The motor bike was very basic, and built as cheaply as possible. I did not purchase any metal, I salvaged all of the metal from the tiller frame and even hand made a custom sprocket for for the bike using a drill press and a hand file. Upon my first test drive I realized the bike had a whole lot of vibrations, and some parts were bending from use such as the clutch arm. The shaft I used was not true and also hindered the bike from performing as efficiently as possible.
So when I went to UC Davis I was exposed to the machine shop and courses such as mechanics of materials, and mechanical design. Which really helped me further improve my bike. I was able to create a custom shaft for the bike from a single piece of steel on the manual lathe in the machine shop. The shaft was a huge improvement in my bikes design and performance. I designed it to so that one side was keyed and I could interchange different pulleys on it. On the other side of the shaft I machined threads to accept bicycle rear freewheel sprockets. And the shaft fit perfectly into a single piece crank bicycle bottom bracket. Below I have a image which shows the old shaft compared to the new and improved shaft. Further more I machined a new base plate for the motor using a manual mill to replace my old one which was made from thin slavaged metal and weakly attached to the frame. The new and improved plate is welded onto two 1 inch square tubes which snuggly fit around the bicycle bottom tube and seat tube. The new plate helped clock the engine to be perfectly aligned in all directions and thus eliminated loss of energy due to a misaligned engine. I was also able to design and fabricate a custom stainless steel gas tank using sheet metal tools, a water jet, and a tig welder.
Overall this build has evolved with my engineering knowledge, and continues to morph into my dream build.
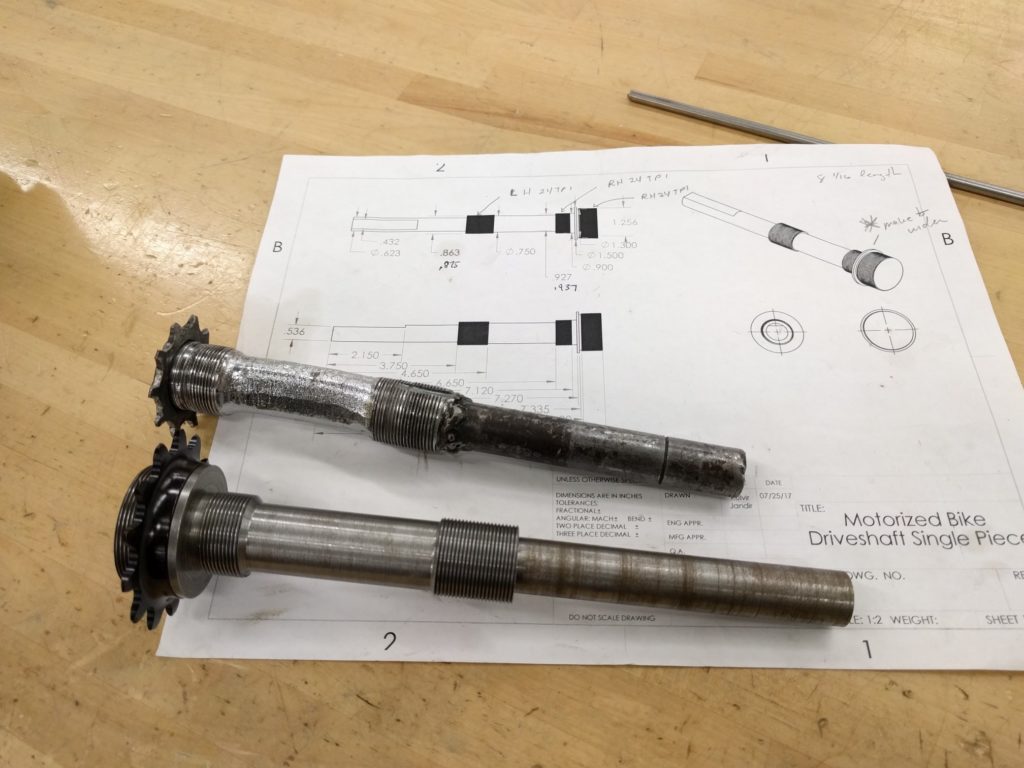
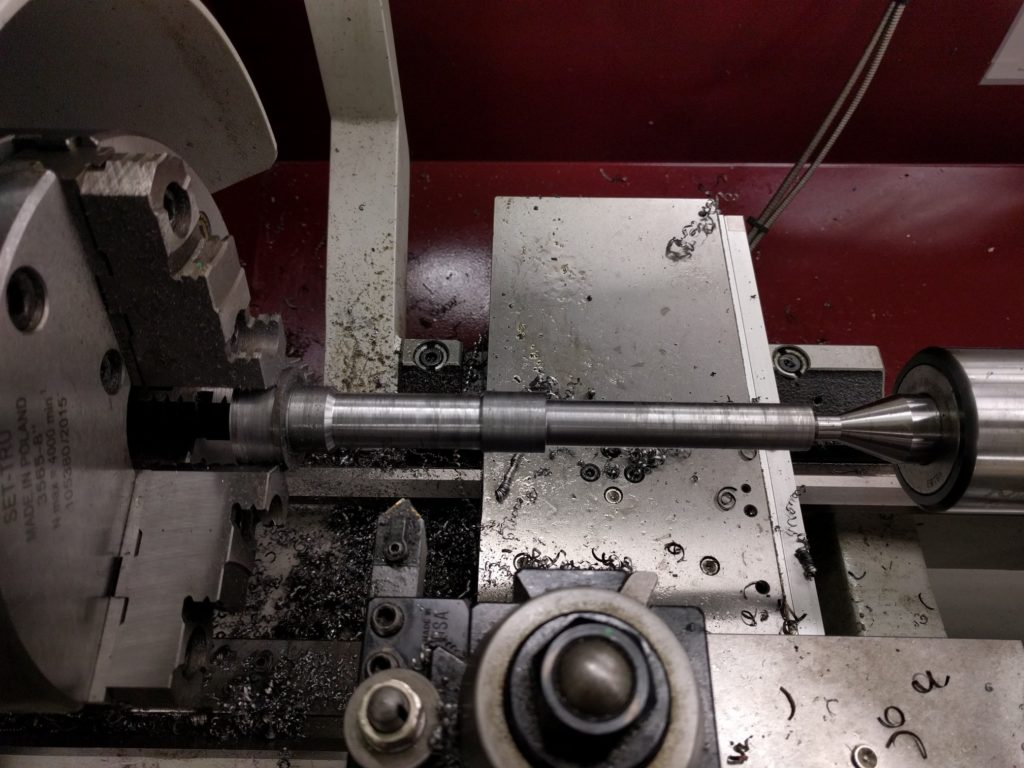
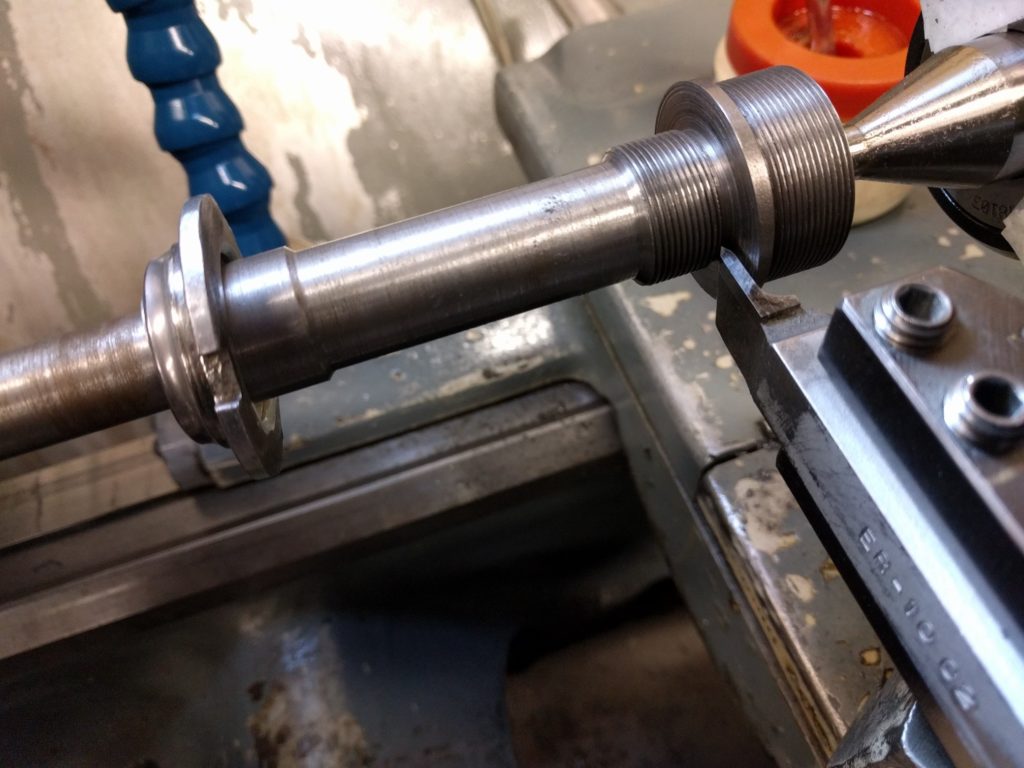
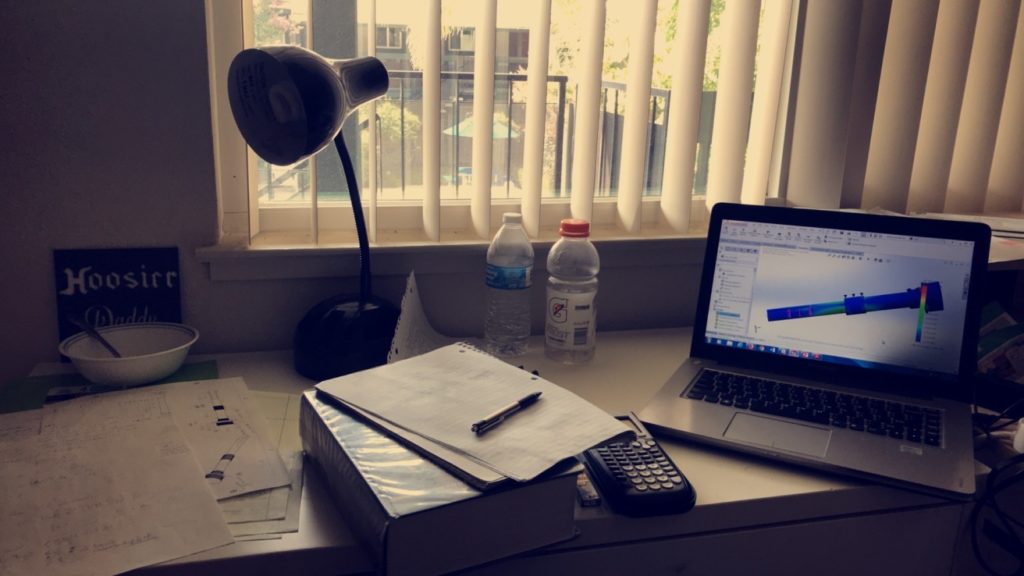
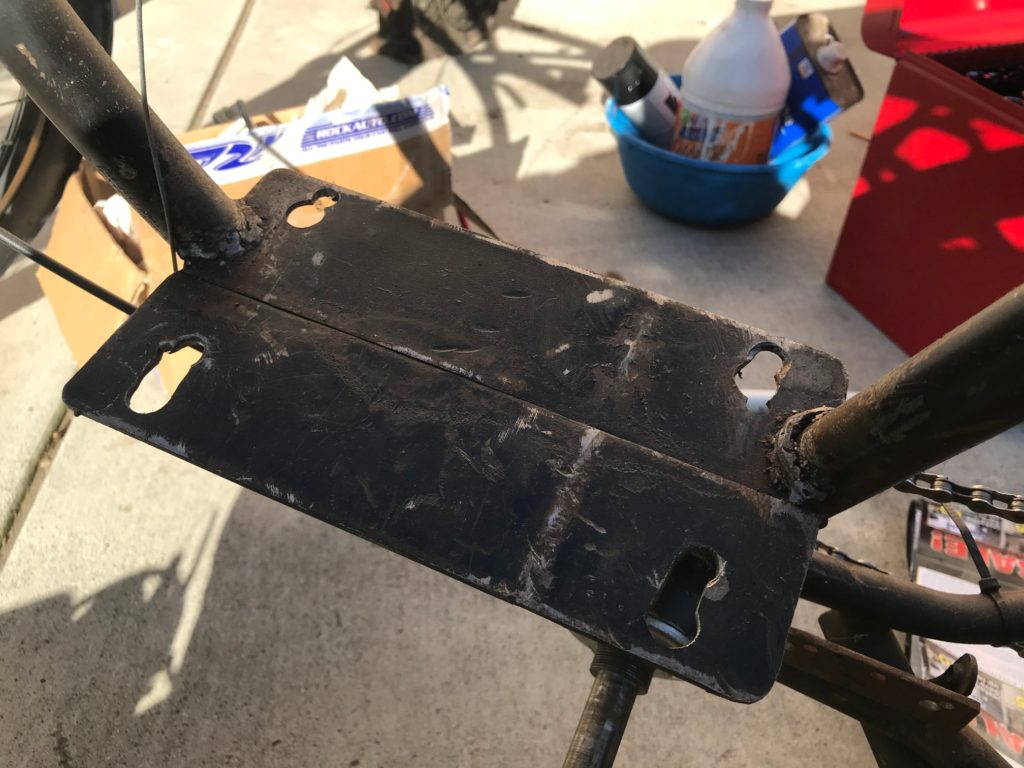
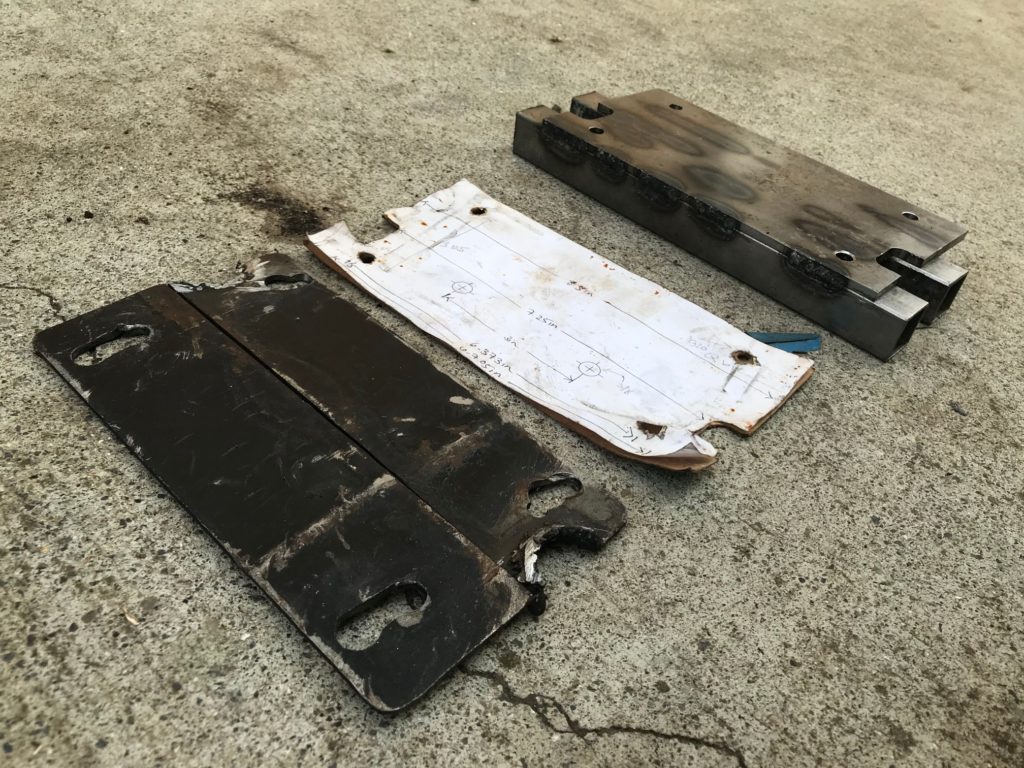
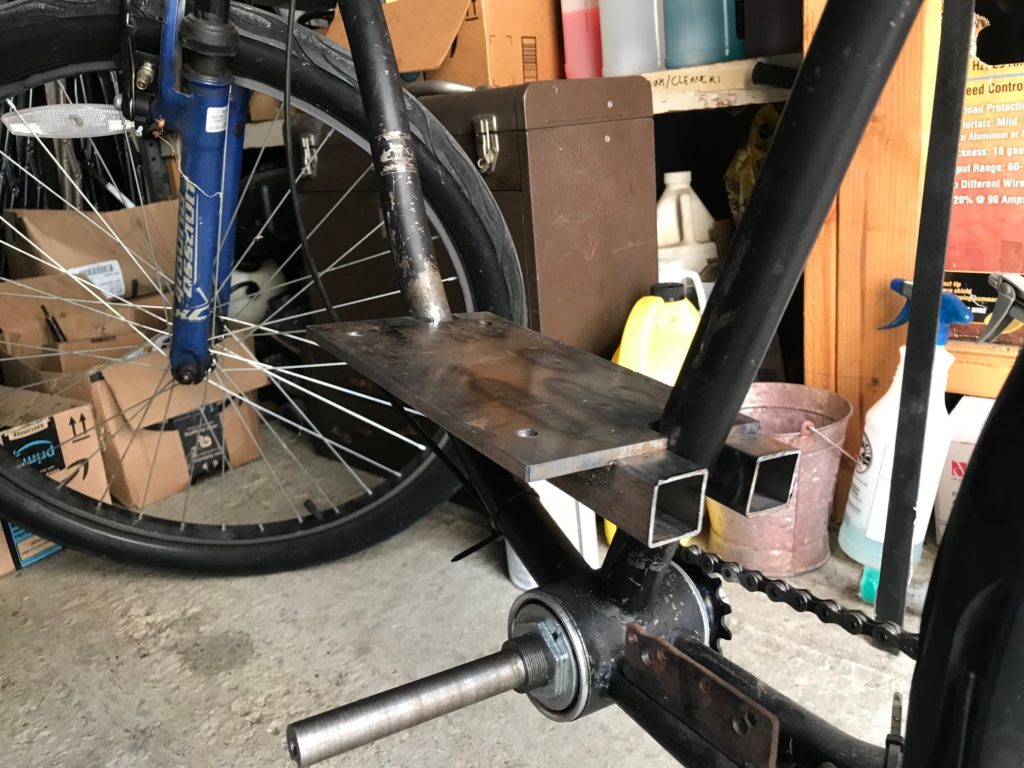
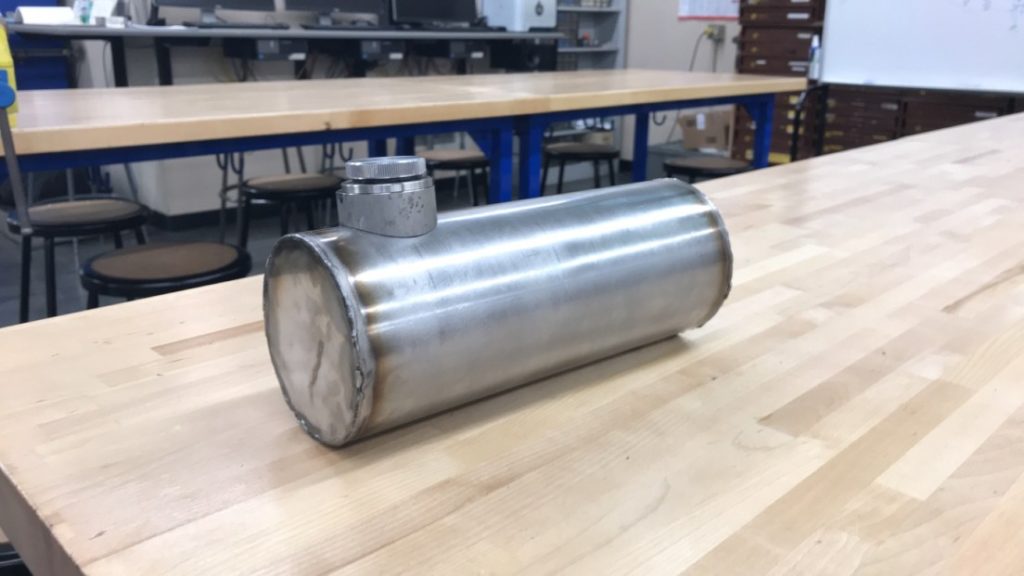
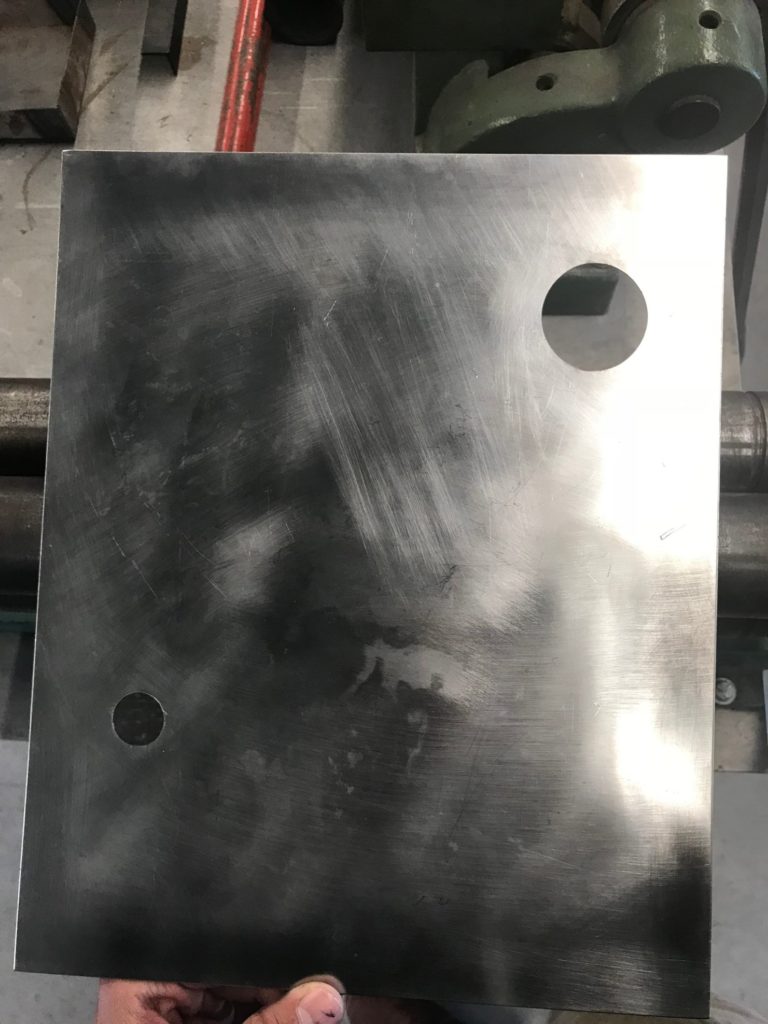
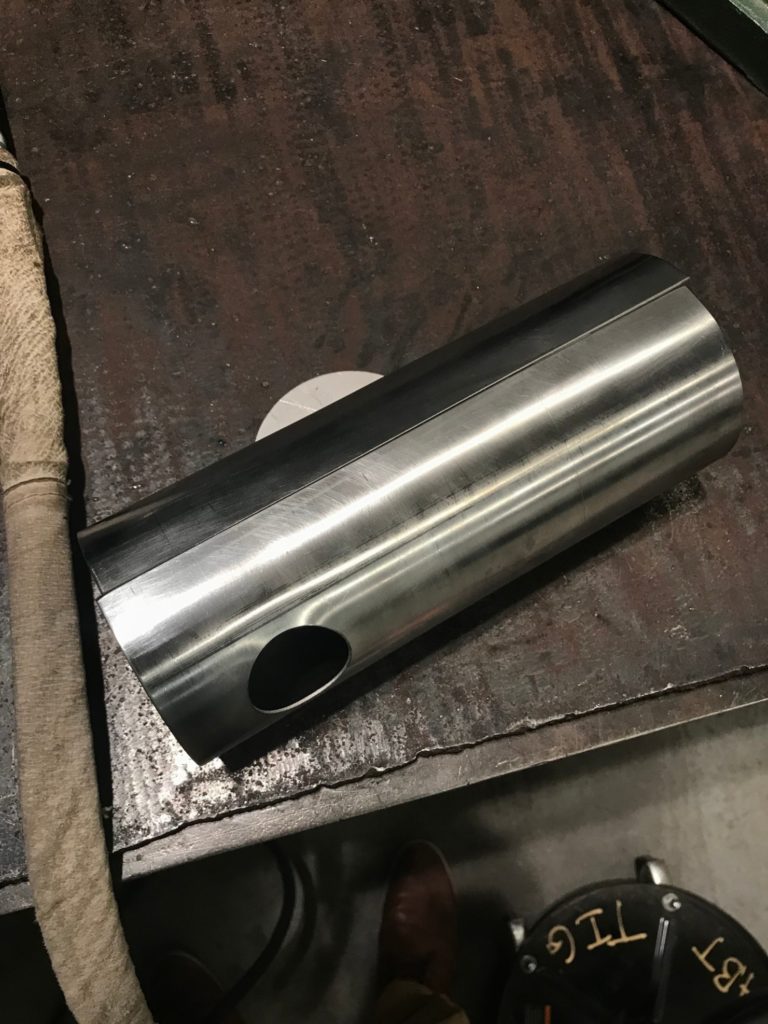
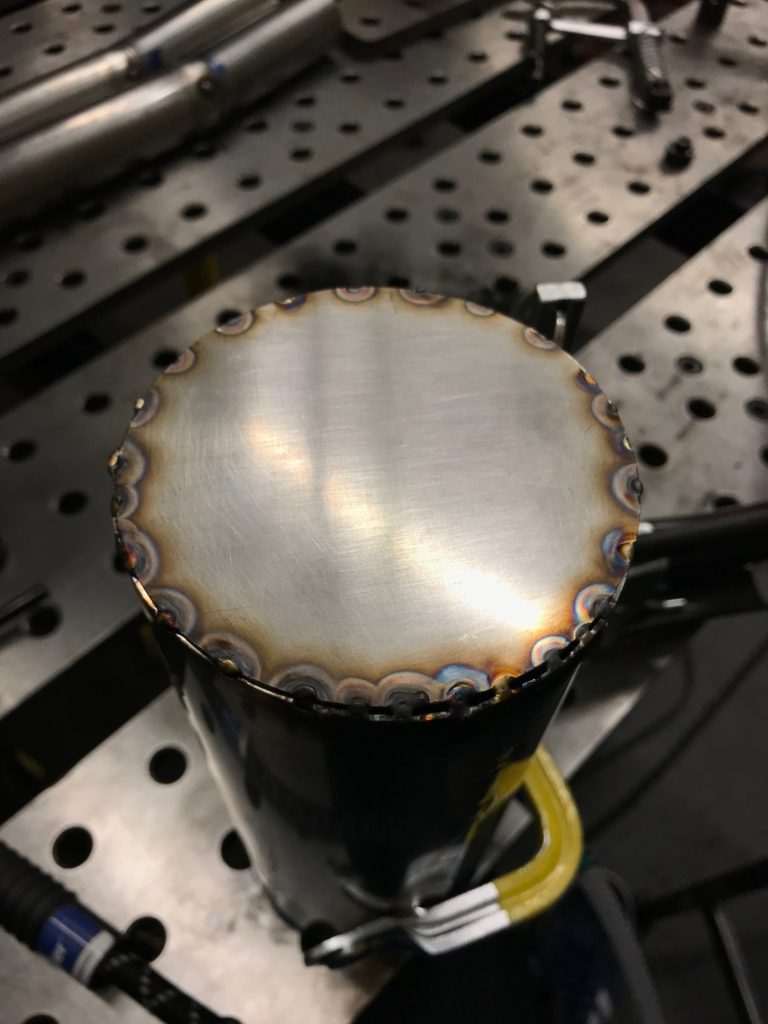
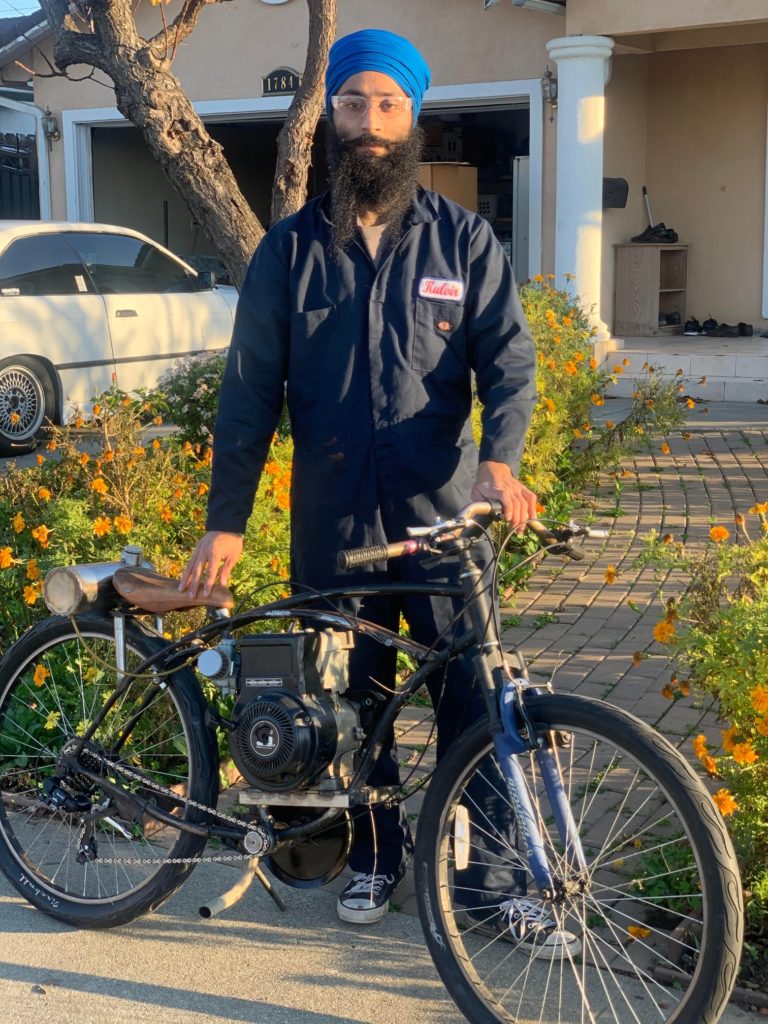